Sometimes you have too much work to do and in order to move fast, you cut corners. You get a couple thousand shirts at the dock, you don’t feel like you have time to count it and then the customer picks it up before you get your final counts. Now the customer gets back to you and tells you they are missing a ton of shirts, but you have no record of what came in and what went out.
Slow down Follow your own processes. Don’t lose money over stupid stuff. We miscounted 1,500 out of a 15,000 shirts and have no way to prove whether we printed them or not.
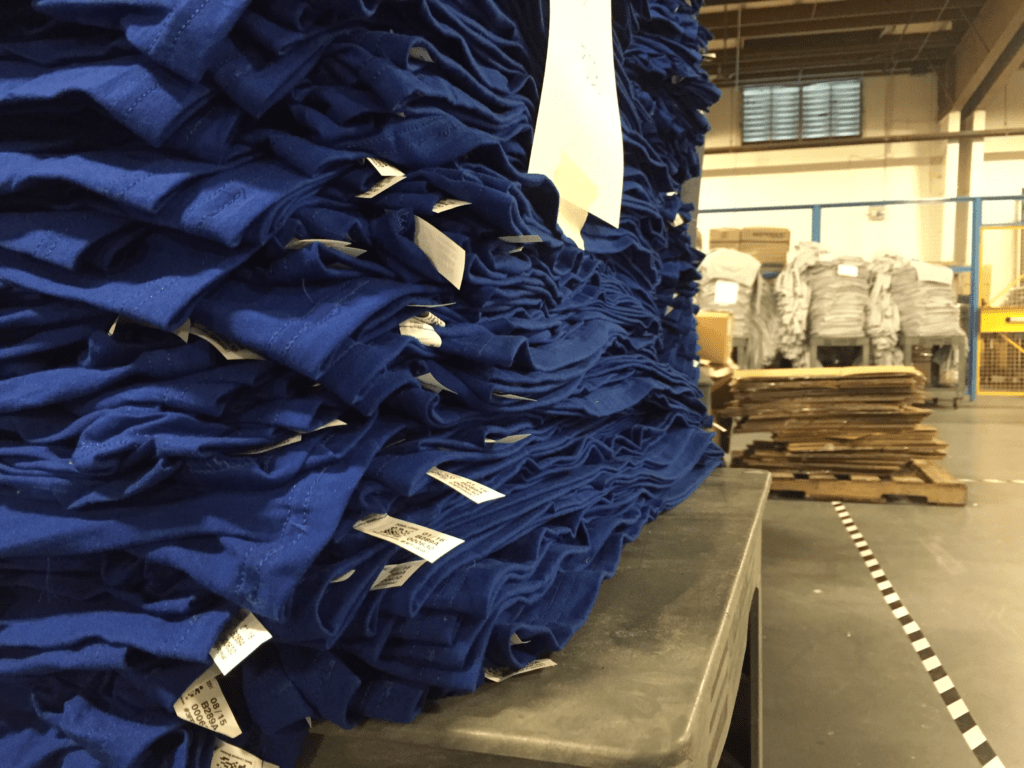
I ran into this problem very early in my career. Since that day I always weighted each box and recorded the size and make of the shirt.
All boxes of each size on larger jobs must have the same number of shirts and one remainder box.
If there is a complaint, I can show the shipped weights as proof.
This is also an internal check because the odd box will stick out.
I also count bundles of 10, not 12 but that’s another story. At a glance I can quickly add how many shirts are in 17 bundles of ten plus 5 extra in my head, I don’t want to figure out 17 bundles of 12 plus 5 loose shirts.