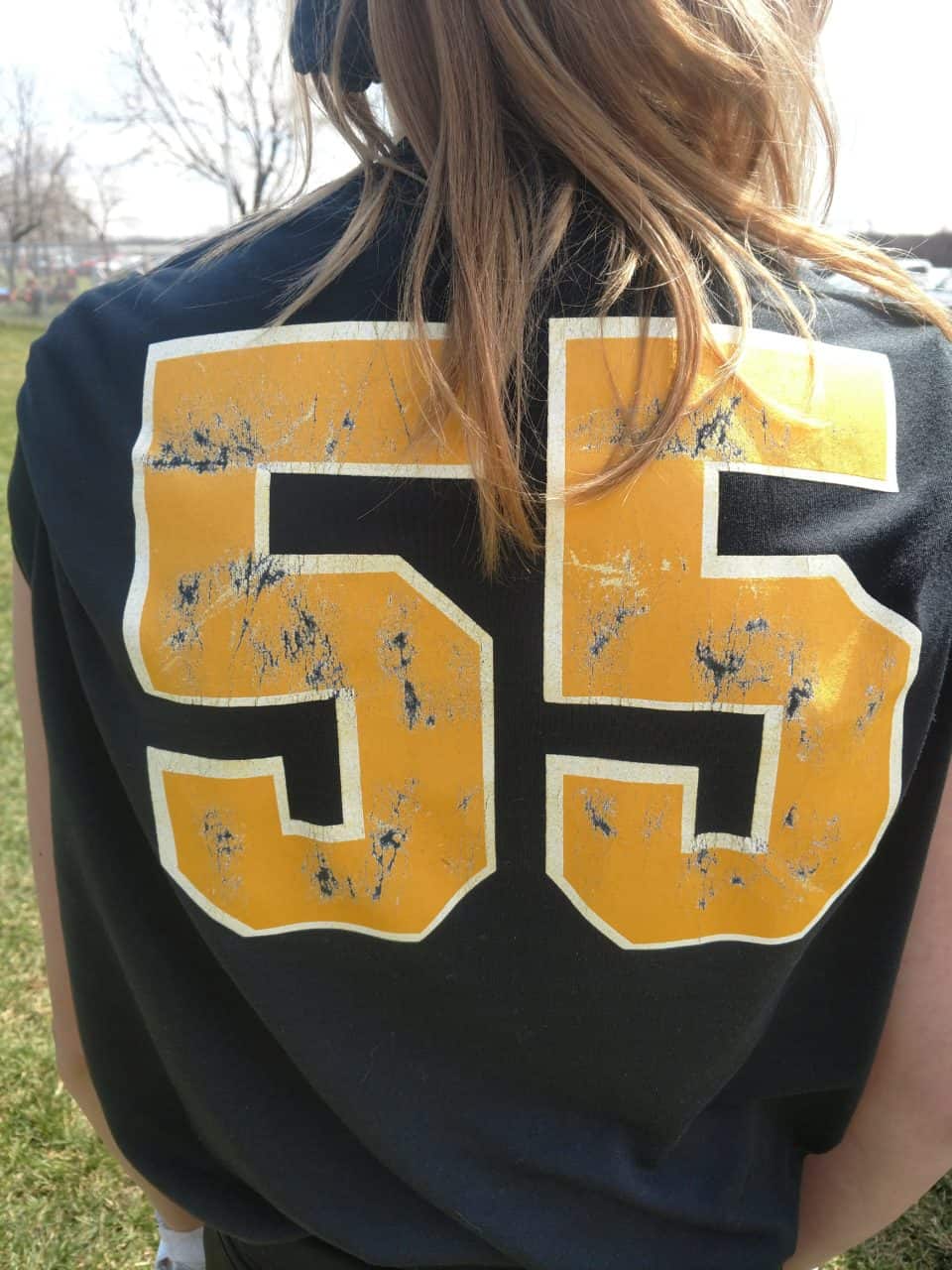
I often get inquiries from folks trying to figure why the ink has washed off their shirts. I wish I had a dime for every time they are sure it is caused by the garment or by overcuring. Sorry, it isn’t. While both of those things are possible, they are highly highly unlikely to happen. Overcuring will make things brittle, but almost never will show the washing off pattern of undercuring. Occasionally a garment will have some sort of finish on it preventing ink adhesion, but that would be rare and again would not show that same ink washing off pattern you see in the photo with this article.
So why is the ink not cured? Often folks will say that they cure ink all the time with the same settings, so it can’t possibly be their fault. Sorry, check again. Here are the possibilities:
1. You never really cure your ink correctly: You think you are curing ink on a daily basis and you are not. You just aren’t checking often enough or were just lucky that nothing is getting returned to you. One friend that is a field rep says he thinks as many as half of you out there are not curing your ink. No joke. By the way, you can use all the devices you want, but in the end the only test is if you wash the shirt and the ink doesn’t come off. Get a washer and dryer at work, or take shirts home all the time.
2. Dryer problem: Something is wrong with your dryer. Its working one day, and another a lead is burned out on your electric panel, the heat probe gets moved by an errant shirt, etc.
3. The Weather: The ambient temperature changed in your shop. Some August days late in the day your shirts start their journey through the dryer at 115 degrees F. and some drafty cold April morning with the heat off it is 40 degrees F. when the shirt starts its journey.
4. Moisture. This is one of the most prevalent problems. Its raining out, the humidity is high in your shop, the truck bringing you the shirts went through five rainstorms, the warehouse the shirts came from was damp. If there is moisture in the garments as the dryer evaporates the moisture, that cools the shirt and causes the ink not to cure. This is especially a problem with canvas bags and thick garments.
5. Shiny: Crows and people like shiny things, but metallics and other shiny or reflective inks reflect the heat, making curing more difficult. Also certain times a dark color shirt will absorb the heat or white shirt reflect the heat, mostly a problem on small electric dryers.
6. Belt Speed: Somebody is in a hurry and curing is a combination of heat and time, and if you turn the belt speed up the ink won’t cure all the way through.
7. Thick ink: The thicker the ink film, the more likely you did not cure it all the way through and if not down to the very bottom of the ink film, it will wash off.
8. Dryer capacity: Sometimes if you have the dryer belt full of shirts it will disrupt the airflow, or put too much moisture in the dryer. It would be a longer article on why that happens and how to build a great dryer to avoid it, but for now know that a full full belt particularly on a small dryer might screw up your cure.
9. Bad ink mix: If you put certain additives in the ink in the wrong balance you can affect the cure. Non-curable reducer for example can nicely thin your ink, but over 1% and it can screw up your inks. Your ink company can give you that information, if your ink company is any good. Its one of the reasons we use Rutland, we can count on their information.
Get all the heat probes, heat tapes and pyrometers you can. Check your dryer speed and temperature. However, always do those things and also do a wash test. The washing machine is the important part of this, it has to wash ok or the ink isn’t cured.
Of the list above, a thick ink or damp shirts are the usual culprits. Next most common is trying to cure lots of shirts with a tiny dryer particularly a tiny electric dryer.
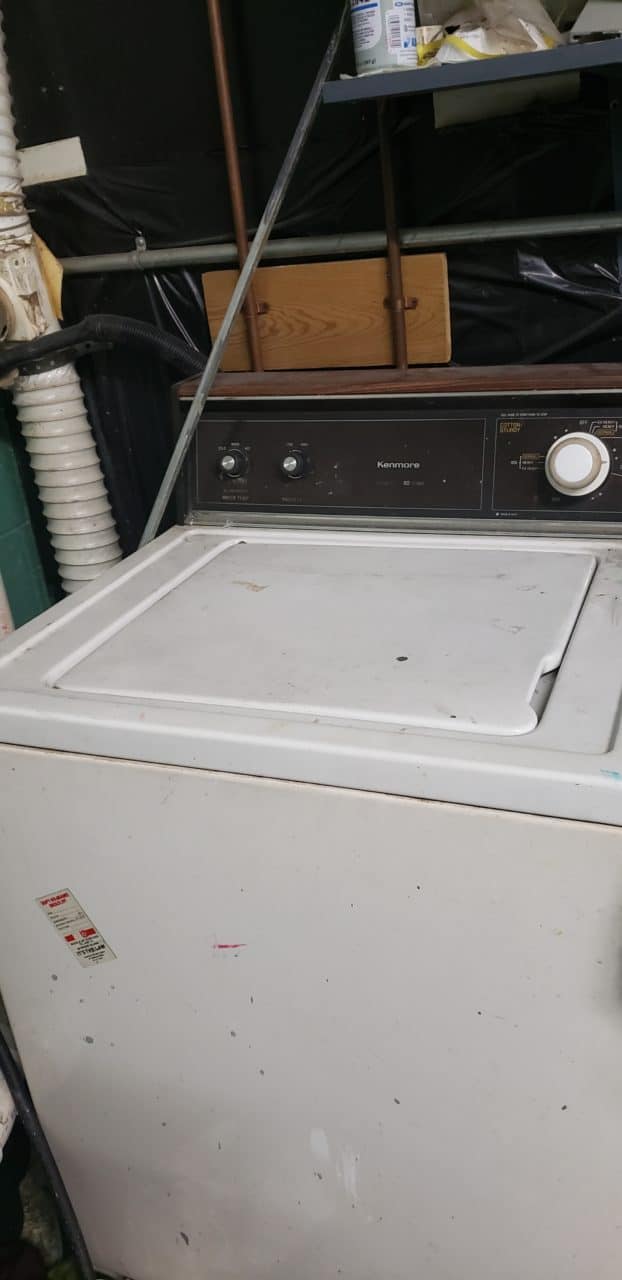
Why are screen printers struggling with benchmark High Thermo-Fusible Plastisol Ink ?
We have been using Fusion 180 ,cures at 180 -260D.F
Fusion Bond cures at 220-240D.F
Fusion Bond Flex cures at 240-280D.F
(Performance properties are same as Silicone Textile Ink
Fusion 180 ink contains only 10% plasticizer overall weight.
Therefore, no concerns for the problems such as undercure, crack ,and washoff
For Automatic Printer Operation, Fusion 180 can be fully cured just with Flash Cure
Unit 450D.F 4 seconds
I love this post. I live in Georiga and the humidity is always high causing daily adventures. We’ve realized that in jobs that require 2 cycles and our dryer gets a little break that sometimes the next shirt we send through doesn’t cure (actually first two because we run two at a time).
We’ve tried everything and continue to tweak things. We have much better luck when we print on high end shirts like Bella and allmade.
It may be that the AllMade or Bella shirts are just thinner, not “better” in some way. Also the AllMade have poly and modal in them and that heats up faster usually as well as not retaining moisture as much in the first place.
We chronically struggle with darks shirts but only with white ink. We print an underbase, flash, print a color, flash, print white, and ONLY the white washes off. The color on top of the underbase stays looking great. But the White printed on the under base washes off. Flash at 220, cure temp – we’ve tested 316 – 338 and still white washes off white underbase EVERY time. Currently using Wilflex Lava Meteor white but thinking of trying Wilflex amazing bright white. Help?
There are a few possibilities here.
It is possible you are overflashing the underprint and that can make for poor adhesion of the top white. The underprint should only be gelled by the flash, so dry to touch, but not cured. I think this is most likely.
The other less likely possibility is that the colored top inks are absorbing more heat because they are darker and the white ink is reflecting the heat. This is not likely, but would be more likely with radiant electric panels versus a gas dryer.
Rick,
Thanks for always posting. I appreciate you !
What do you think is a minimum dryer chamber ? I have a Anatol gas dryer, with a 6′ chamber. What should be dwell time in dryer ? I occasionally get under curing of ink on poly/rayon blended shirts, and if I increase temp, I scorch the shirt. Can yoy offer me some help ?.
We just started doing shirts and only have a flash dryer. Our ink is washing off which now I think is because we did not let the temperature get hot enough. We mostly use Bella and Gildan shirts and we have Nevertheless plastisol ink, we are going to use the flash dryer at 320-330 degrees for about 1 minute. My question is, does that sound correct and is there a way that we can recure the shirts we already have finished from weeks prior?? Please help!
You can reheat the ink to cure it.
The entire ink film has to cure to 320, a minute at 320 doesn’t sound long enough to get all the way through. Either turn up the heat (but watch out about scorching the fabric of the shirt) or increase the time. Besides the thickness of the printed ink the other factors are if the ink reflects the heat (white ink takes longer than black ink) and if the shirts have moisture in them.