We received a panic inquiry from a supplier that we work closely with. They had a customer who claimed that they could not get their prints to cure on a canvas bag. We field many questions for our vendors, since printers love to blame the substrate for printing problems, so our vendors use us to do the detective work.
In this case the bag company’s customer said that the ink ran when the printed bags were washed, despite the fact that they “ran the bags at the highest temperature of the dryer.”
Curing plastisol ink is always a function of time and temperature. Curing ink on canvas is sometimes tricky. Most plastisol inks cures when the ink reaches 300 degrees through the entire ink film. Getting it to 300 degrees is the issue.
Canvas provides a challenge because if it is a coarse texture sometimes the ink film has to be very thick to get good coverage. If you normally run your dryer at a certain temperature and speed that regularly adequately cures the ink, it may not cure this thicker ink film. You may have to turn up the temperature or more likely slow down the belt. Just turning up the temperature may scorch the canvas, so ideally you give it more time instead.
The problem I have seen more often with canvas is that because it is thicker than t-shirt jersey fabric it can absorb a great deal of humidity. You can’t see the humidity or even measure it but in humid or rainy weather you just have to assume the canvas has moisture in it. That exposure to moisture could happen at the mill, at the distribution warehouse, during shipping, or in your shop. This moisture can cause big problems. Basically what happens is that when put through the dryer, the water evaporates and cools the canvas, just like why we humans sweat to cool ourselves. This cooling is in direct opposition to the heating of the ink. The evaporation cools the canvas and so the ink doesn’t reach its curing temperature.
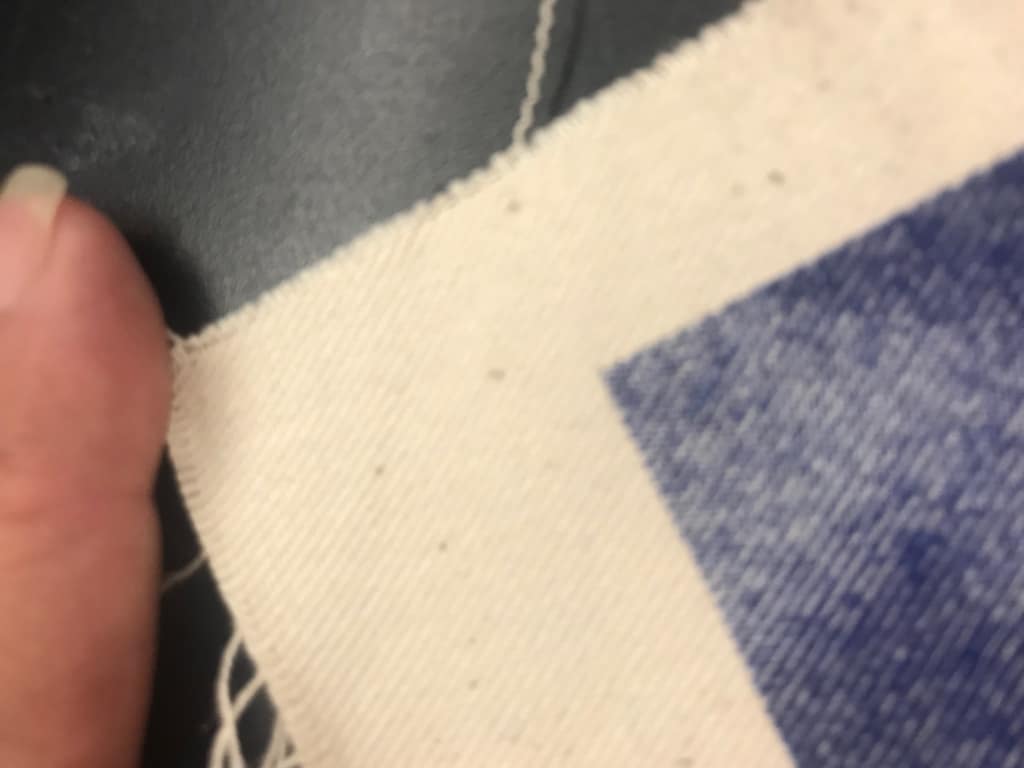
So what can you do about it? You have to get the water out. If you are doing this all the time, you better have a long heating chamber on your dryer so there is time in the dryer to get the water out because once the canvas dries, the ink can get up to temp and cure. Barring a long dryer run slowly, you can put the canvas through the dryer one or two times before you print it. And if it is damp in your shop, then cover it up with plastic until you print it, or it can reabsorb moisture again.
We used to print some very thick 18 ounce canvas with lots of ink coverage. To be sure of a cure we would run the bags through the dryer before printing, then print them, and then run them through again once or even twice.
If the ink is not full cured it also has crocking issues. You can take a piece of a white t-shirt and see how much ink comes off if you rub the print. You almost always get some crocking, but over time you will recognize what is an acceptable amount.
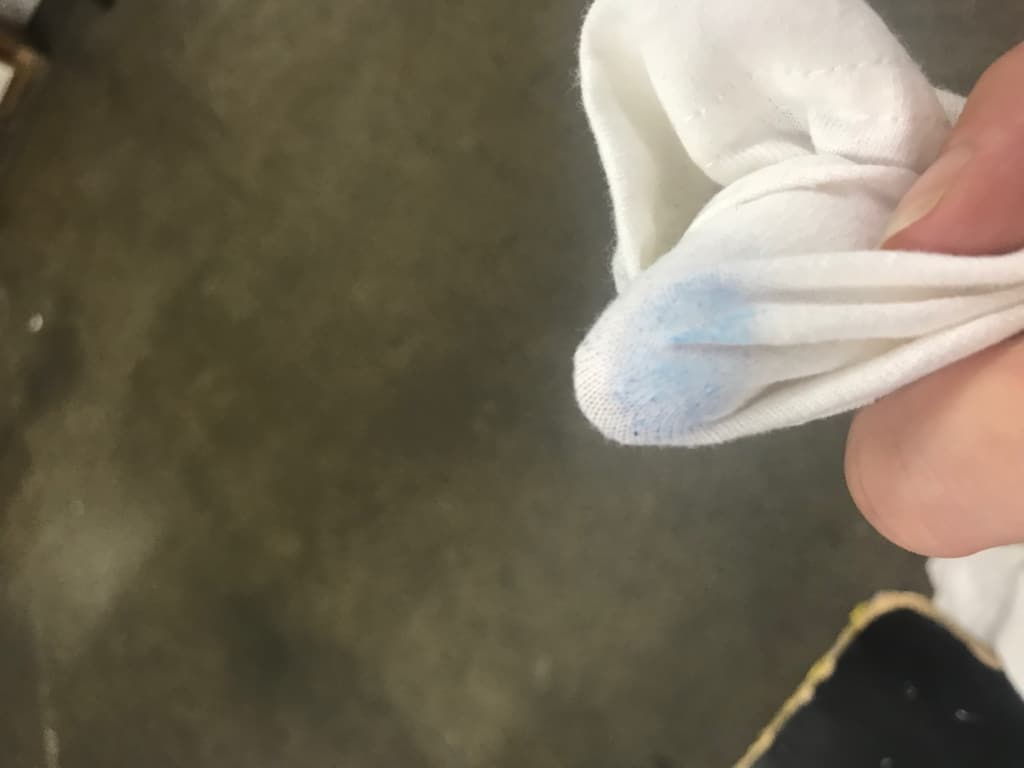
You can get all kinds of temperature testing equipment, but putting the canvas through the wash is the best way to check for ink curing, so always wash your bags if you are at all concerned about the ink curing.
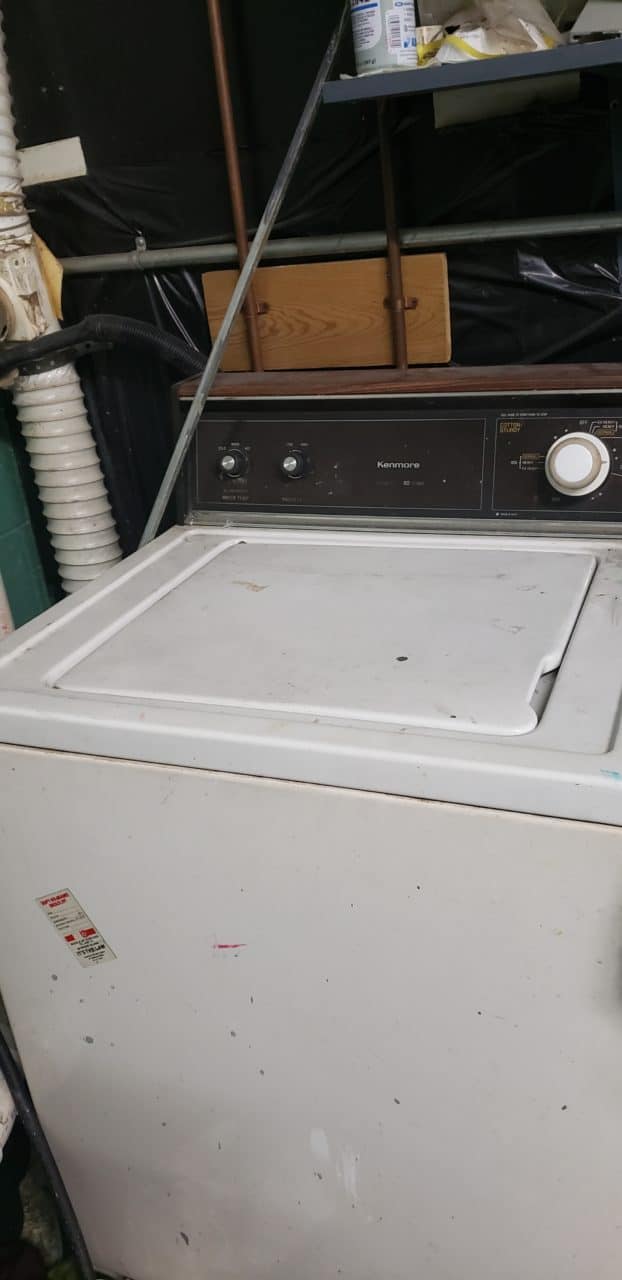
So back to the bag company’s customer… We got them on the phone and it turns out they were printing on a damp day and they only had a relatively short electric dryer, and one with not the greatest airflow. They had to run the bags through three times in total at a slow speed but in the end they did get the ink to cure and they also realized they were not dealing with bags that were defective in any way.
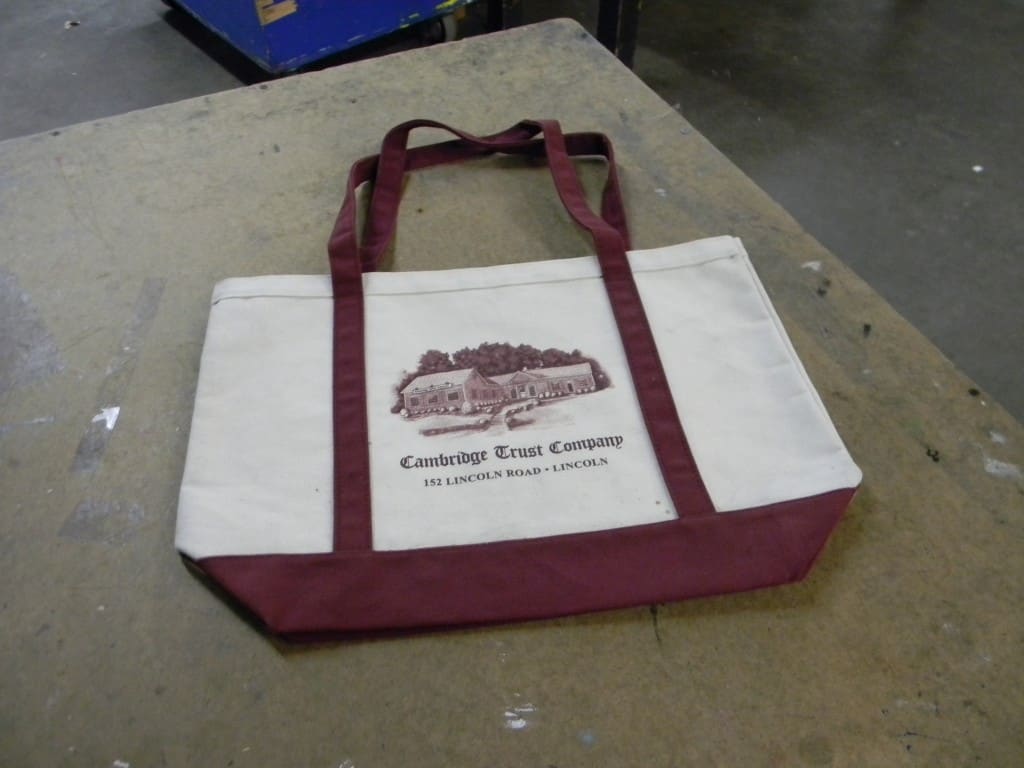
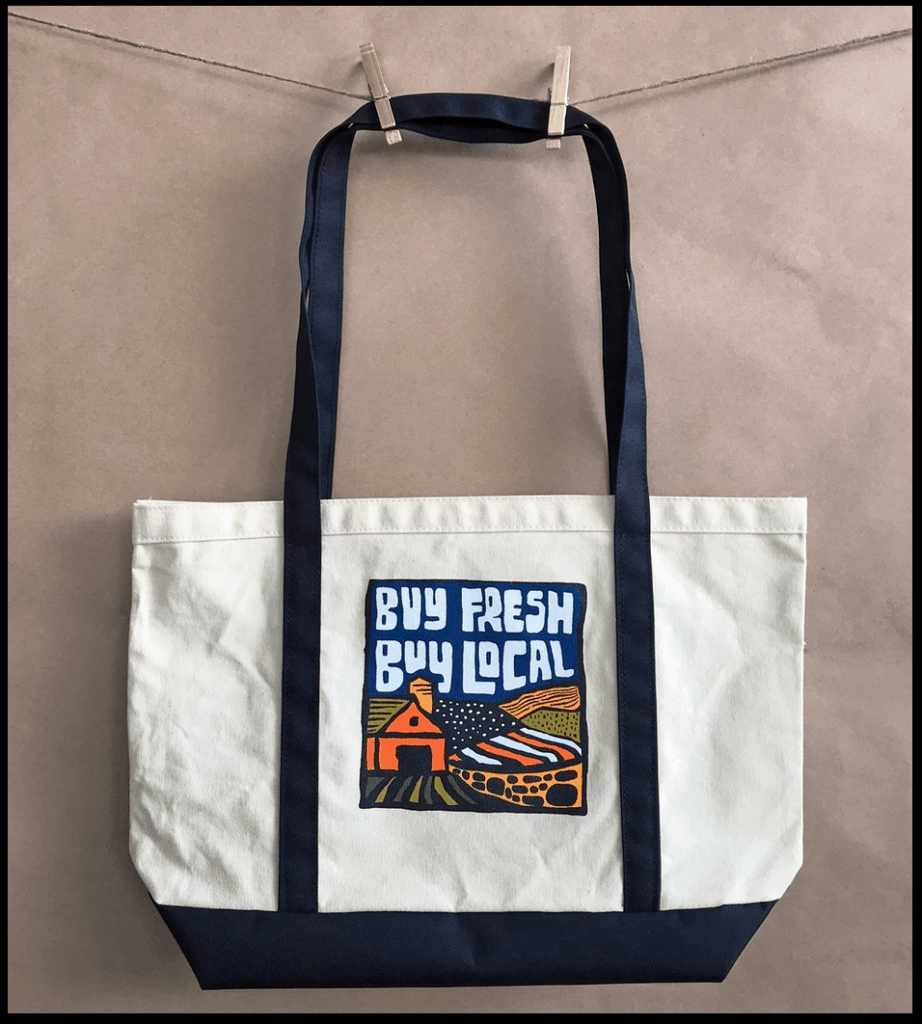
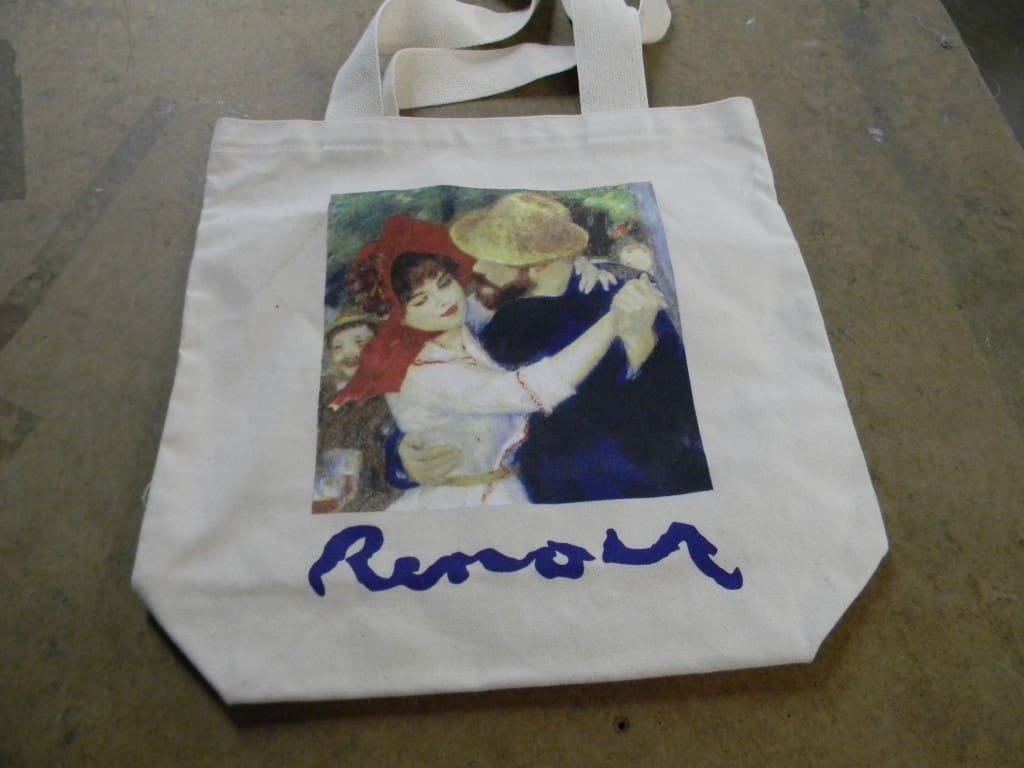
Comments