What do you do with all those mis-prints and/or defects? Most shops just turn them into test prints and then into rags, right? What’s the matter with that?…
As a contract decorator we have a responsibility to our customers to handle their product in a professional and accountable manner whether it’s before, during, or post production. Here’s how its done:
– During a print run misprints and defective garments (most of which are found in receiving) are set aside for inspection post production
– At the end of a print run these items are inspected and verified as spoilage by our packaging department and is accounted for by size, style, and quantity
– Spoiled items are then placed in a clear plastic bag and labeled by order number and date
– This bag is then placed in a box labeled: MISPRINTS/DEFECTS
– When the box is full it is sealed, dated, and sent to onsite storage
– Eventually after a couple of years the spoiled good will be donated (with customer consent of course) or used as test prints (a practice that I intend to stop in the near future, but that’s another post)
This protocol is so important as we at times will have to reference the physical mis-prints/defects for both internal and external purposes. We have resolved customer/end-user disputes, used it to support disciplinary action with employees, and used it for training/education of both employees and customers.
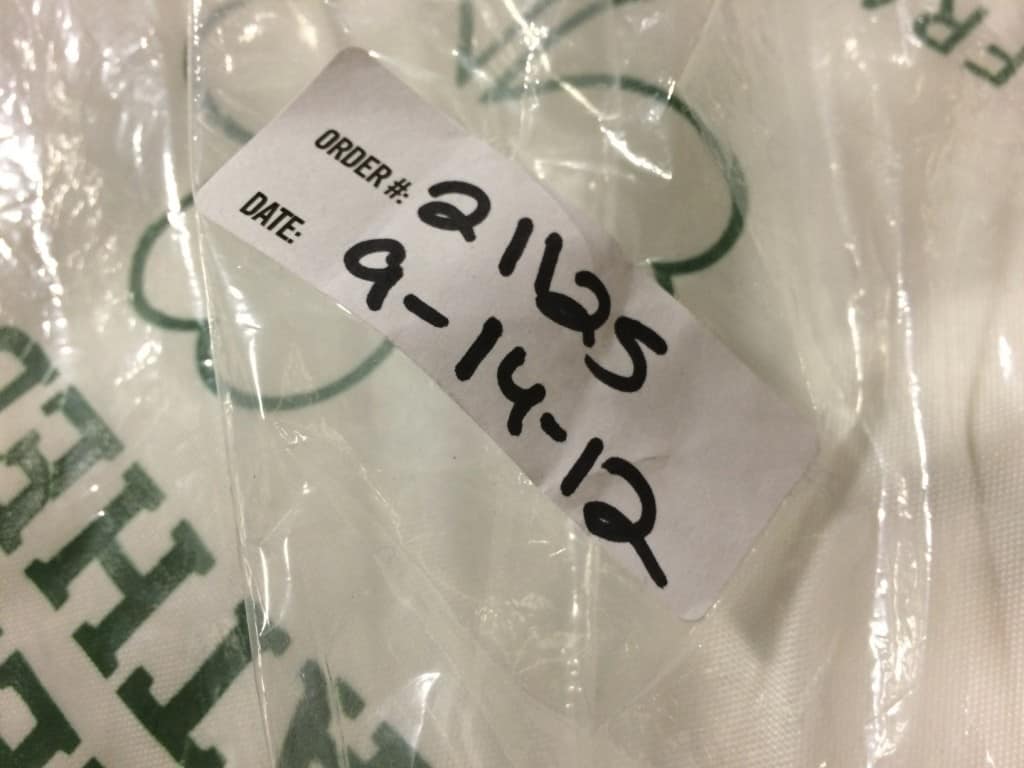
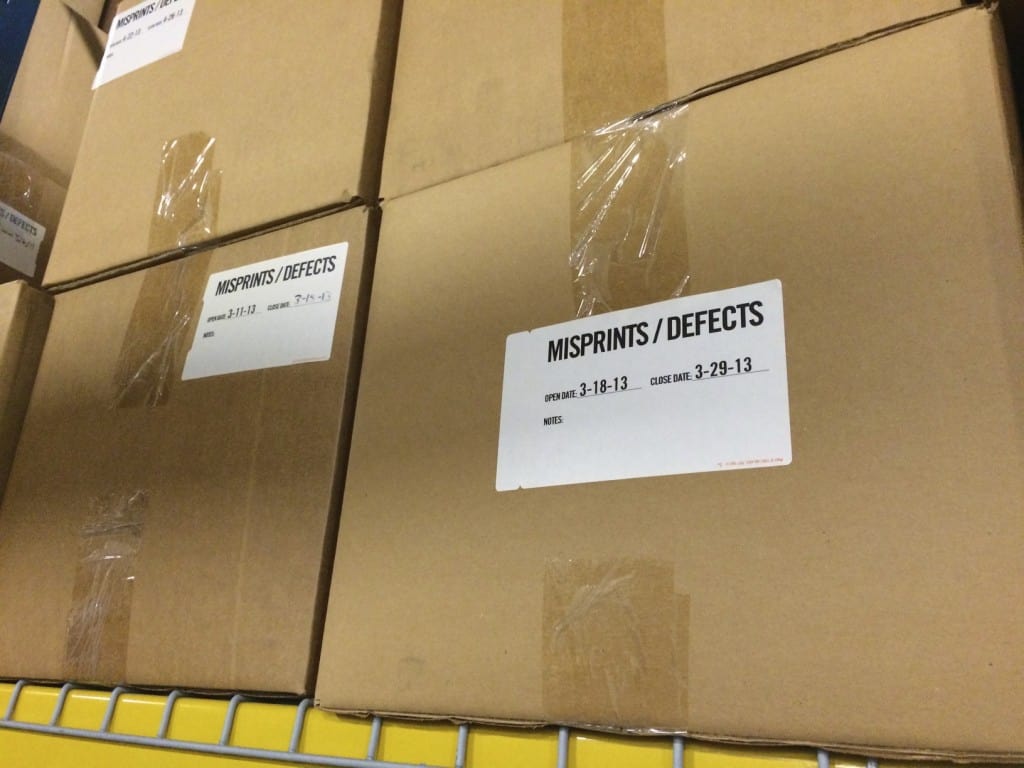
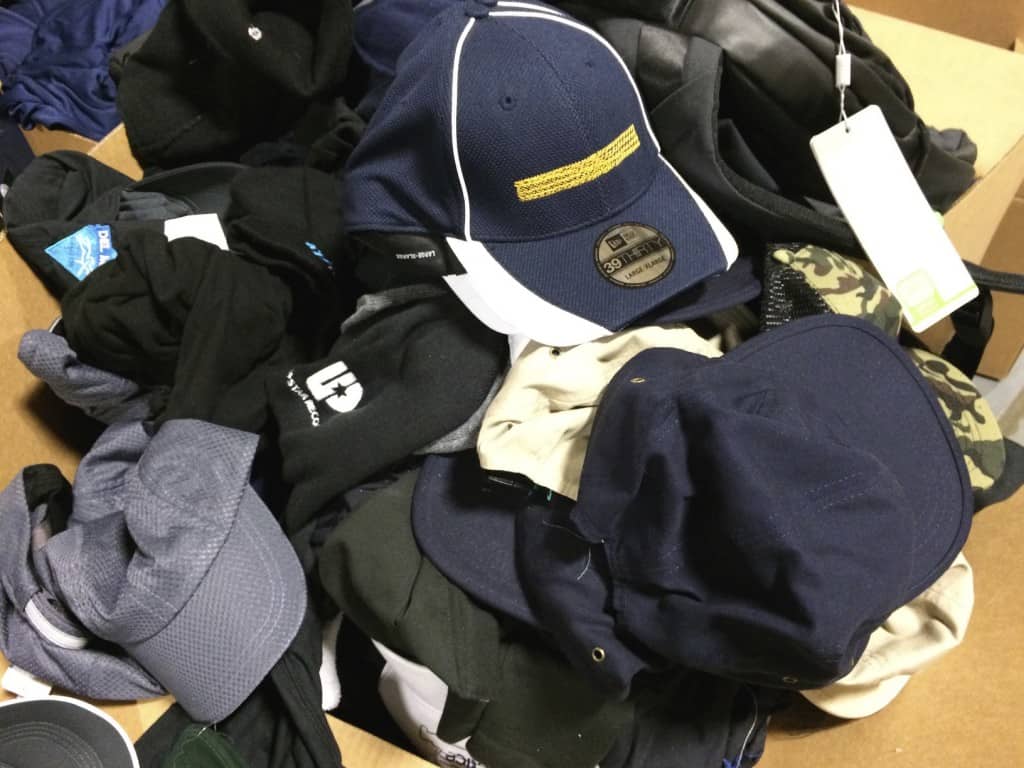
Comments