When I started my shop years ago I never would have guessed that we would do in-house re-labeling to the extent that we do today. In fact, we didn’t even touch our first re-labeling project for a few years after opening our doors. For that first project, we cut out woven tags from stock tees, printed cold peel transfers and heat pressed them onto the interior of the shirt. Today, re-labeling has become an integral part of our service. We re-label thousands of units on any given day. We now offer heat transfer relabeling, woven tag re-labeling, and screenprint re-labeling.
Re-labelling can open the door to working with customers that absolutely require their vendors to retain this capability. The total investment to offer all three versions will run $15k – $20k, and that’s for new equipment.
By far the most common form of re-labeling for us is screenprint. This is also the most profitable form of re-labeling. Yes, I said profitable. Think of it this way: a top-of-the-line label press will run you approx $12k brand new and a single operator paid $15-$20 hourly (including taxes and insurance) can run 500 units per hour (assuming tear-away tag) at a going rate of $0.25-$0.50 per. Assuming an average charge of $0.37 per, you can comfortably generate $185 per hour. Less labor and consumables ($0.03 per and that’s probably on the high side) you can gross $150 per hour. Not bad at all considering the small footprint of the relabeling operation.
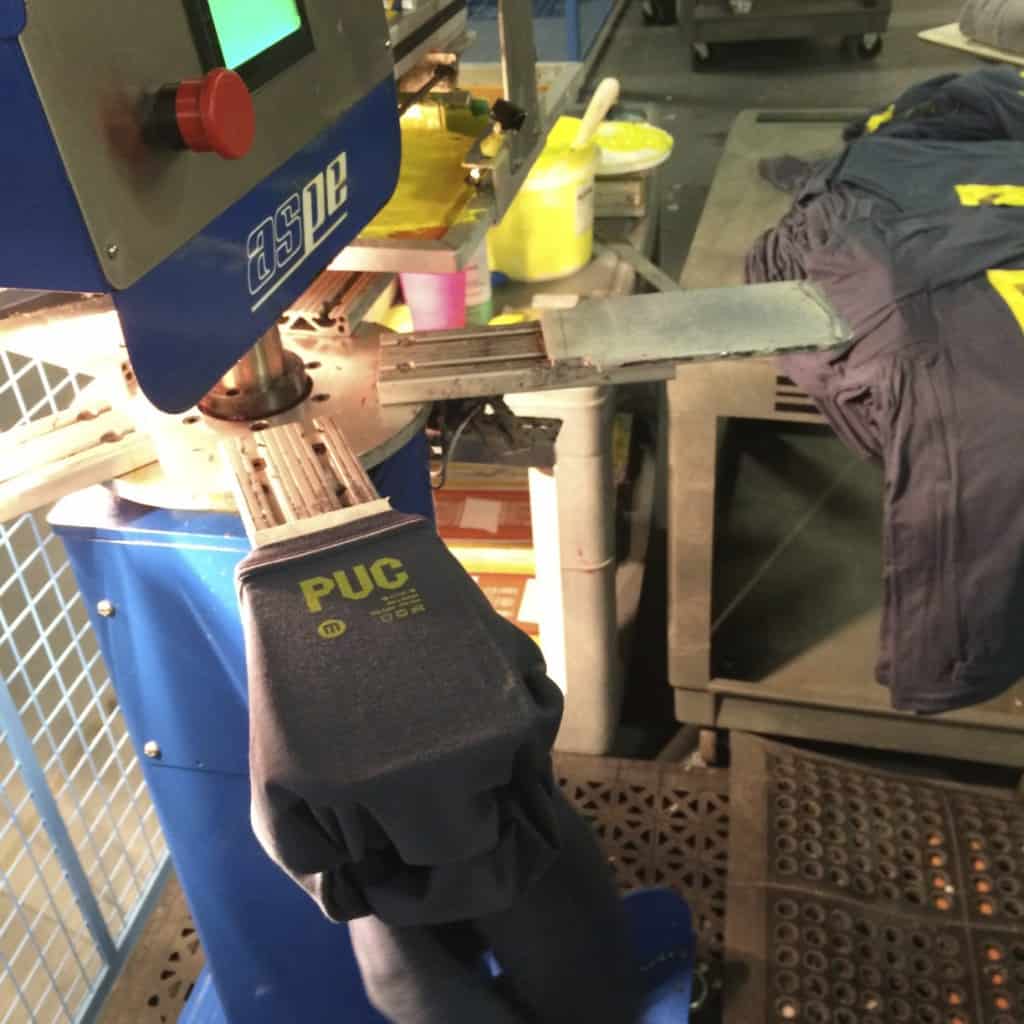
Our second most common form of re-label is traditional woven tag re-labeling. This is a more intensive process which requires an operator to cut the stitching on the interior neck tape, remove the existing label, and replace with a new label. You can count on getting $0.25-$0.50 per ($0.25 per is more likely) for this service but you will need an experienced sewer and they will only average 200-300 units per hour. A top-of-the-line industrial sewing machine will run $2000-$3000. So there is a low cost of entry but it is a slower and more labor intensive process which requires greater skill.
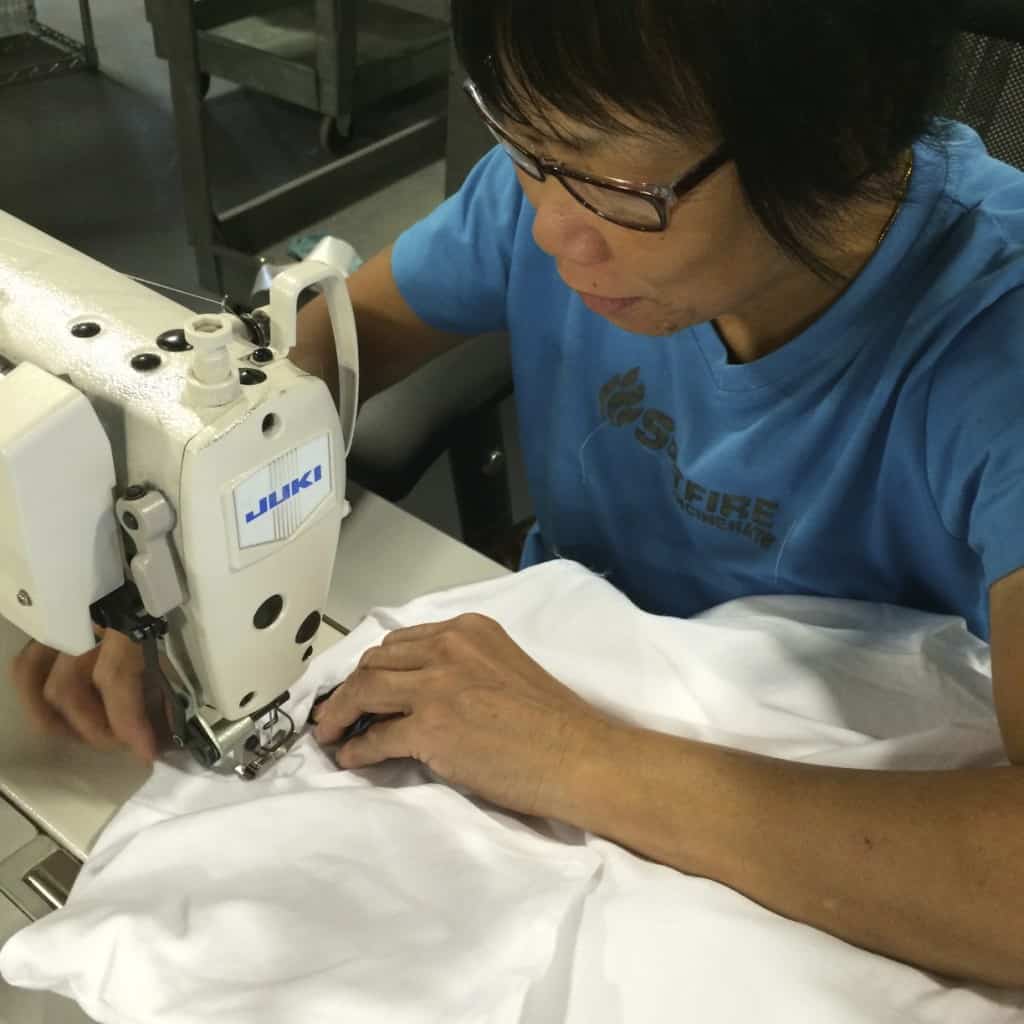
Lastly, there is heat-press re-labeling. Quite honestly we almost never use this method. But, from time to time customers will supply us with heat transfers which we then apply with a label transfer heat press. Assuming a tear-away tag, you can count on a single operator producing about 300 units per hour at a going rate of $0.25 per. A top of the line label heat press will run $3k-$5k.
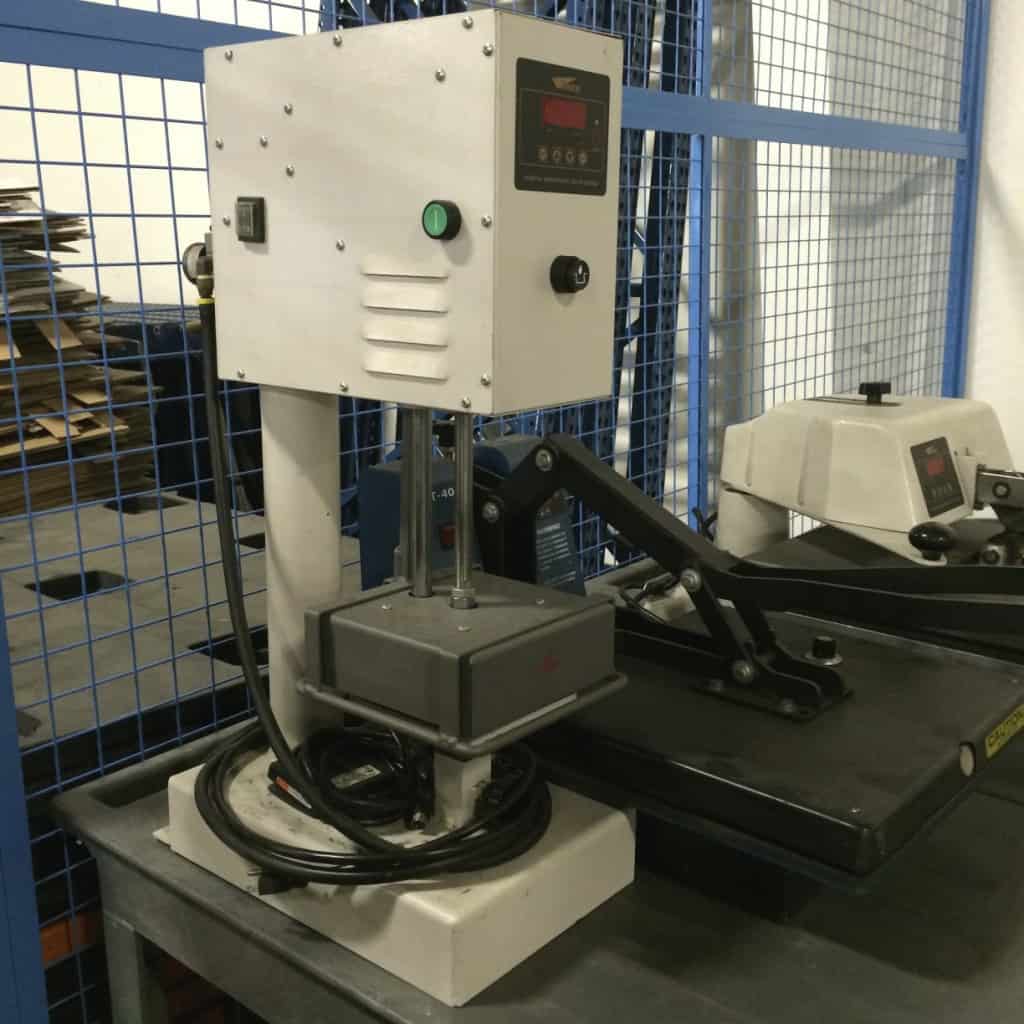
Going all-in on re-labeling certainly created opportunities in working with retail lines for my shop, and it has also become commonplace with corporate/promo apparel these days. I expect the demand to grow.
Bottom line: If you are serious about screenprinting, get serious about re-labeling.
If you are planning to sew in new labels, research fold types. The “Manhattan Fold” labels are easier to handle. The small additional cost will be regained during installation.